The first thing I did was obtain a couple of 16.5" brake drums from a large semi type truck. I put them on the lathe at work and machined the drums so the open edge of the drums would mate with each other.
Here is a pic of the lathe I used; it took about 2 hours to do both drums. It is also available to me during off hours at work.
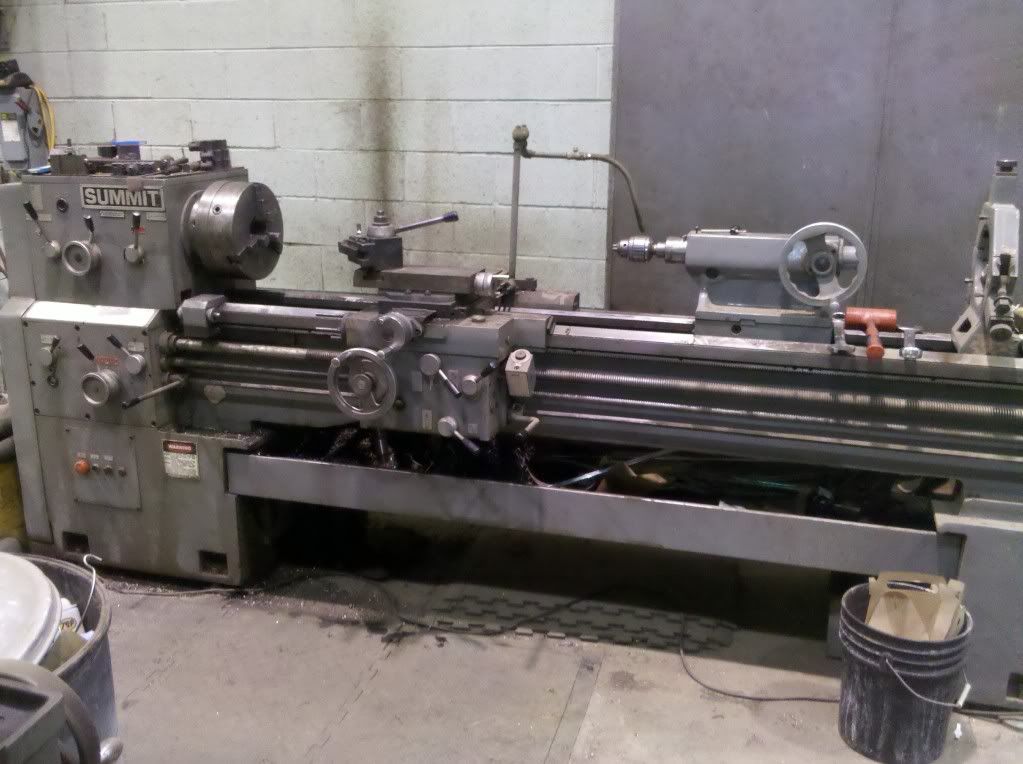
The drum edges, they are orange looking because of the fresh rust. I kept these in the back of my truck for a week while I gathered parts.
The outside cut on the bottom drum.
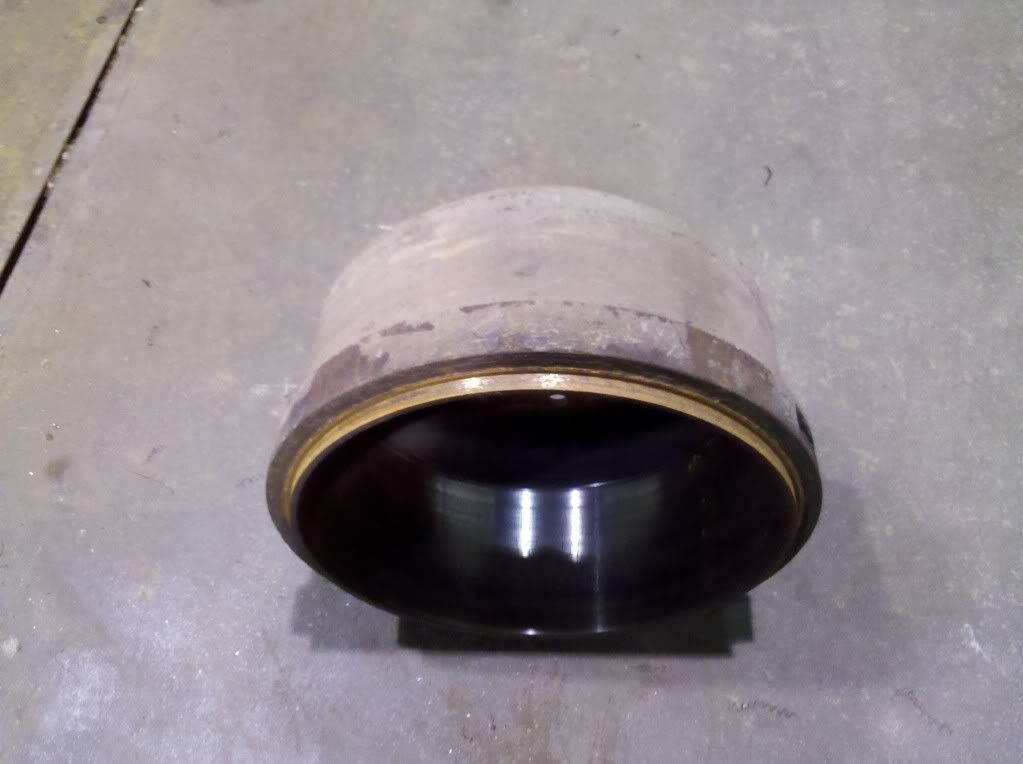
A close up of the inside cut on the top drum. Sorry for the pic quality.
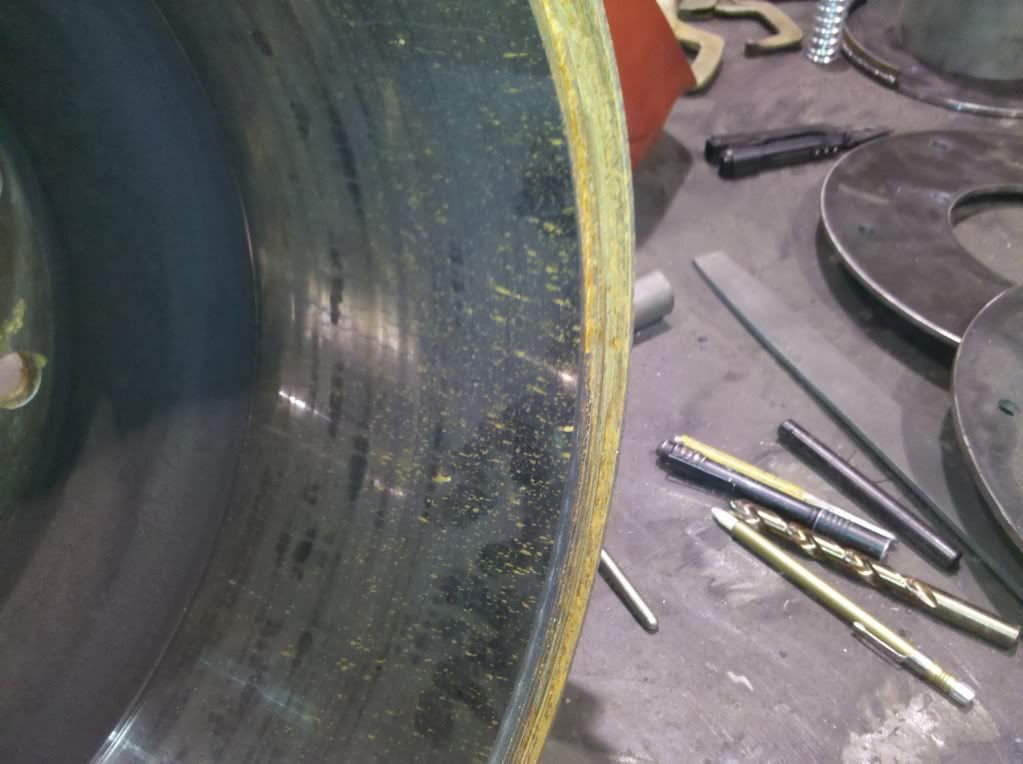
The cylinder after sandblasting and removing the bottom 2 inches, I believe it came from a C-15 Cat engine. I cut the bottom flat and inside of the cylinder with the lathe. I cut the inside of the cylinder about .020" because that area seems as hard as diamonds and does not drill well. The air vent holes will be in the lower 3" of the cylinder.
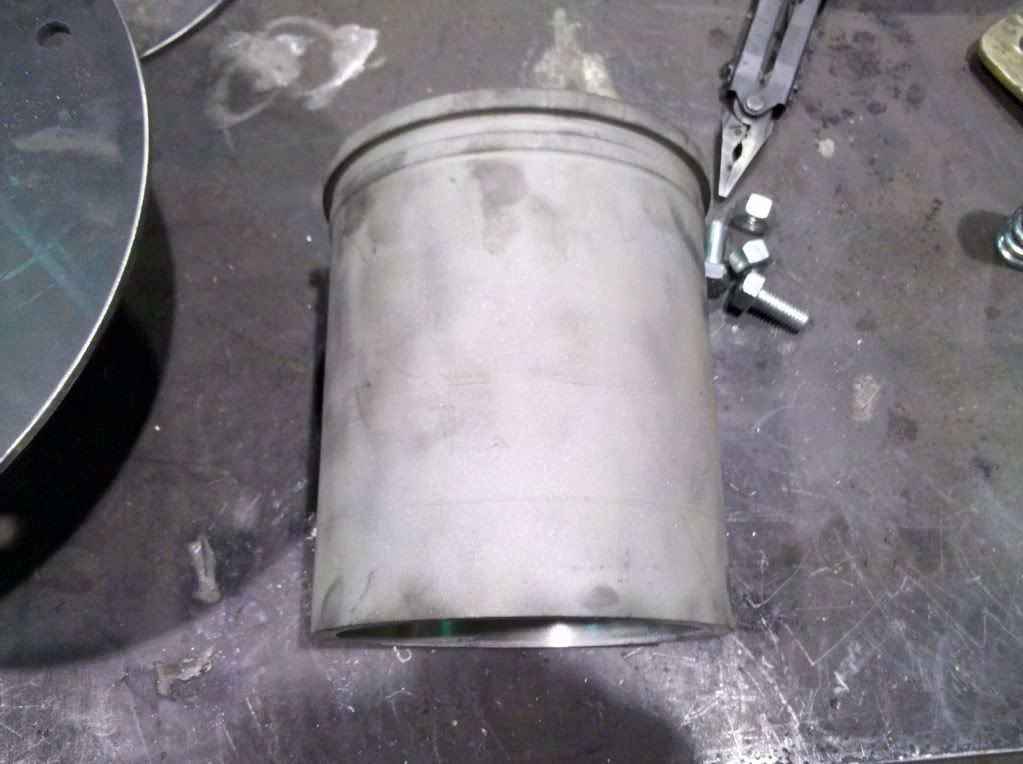
I cut 2 round plates to fit on the lug side of the brake drums. Both plates have 5- 1/2" holes for bolting. There are more holes, two for the bottom plate to fasten the cylinder to.
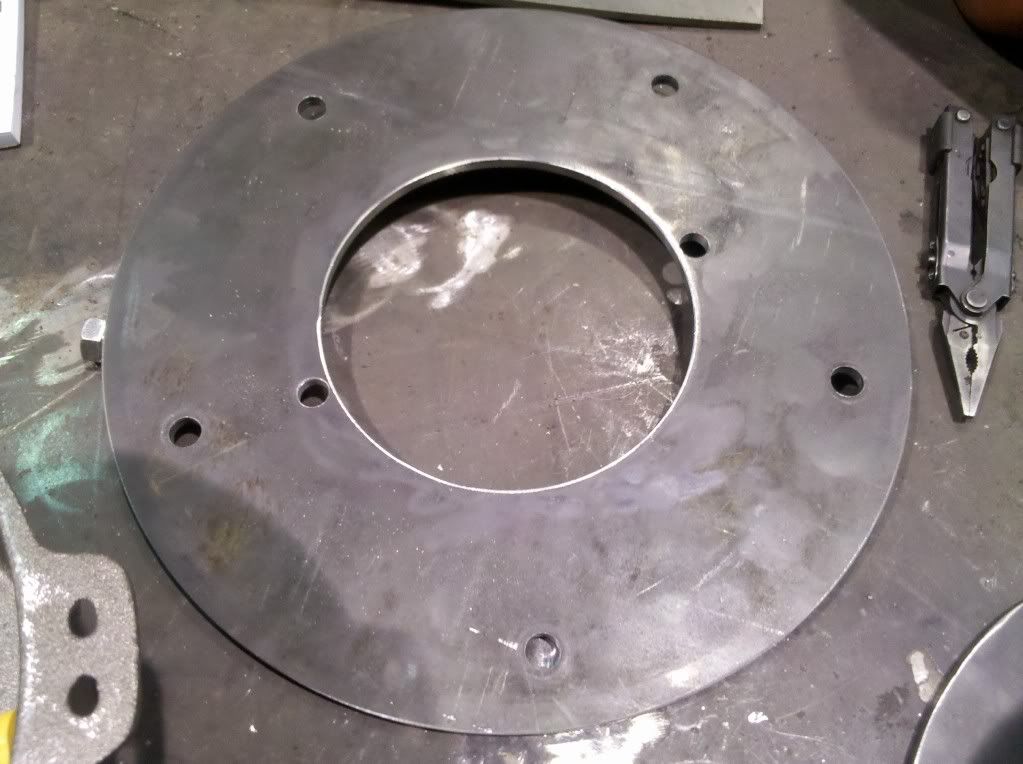
This pic shows the top drum with the second plate on top.

I cut another disk. It will set on top of the cast pot. The pot is the place the oil will drip into. The disk is machined so the cylinder will fit into it. The cylinder is about 6" O.D. The disk also has 5- 1/4" vent holes and a piece of steel welded to it, to help position the pot.
Here is the pot.
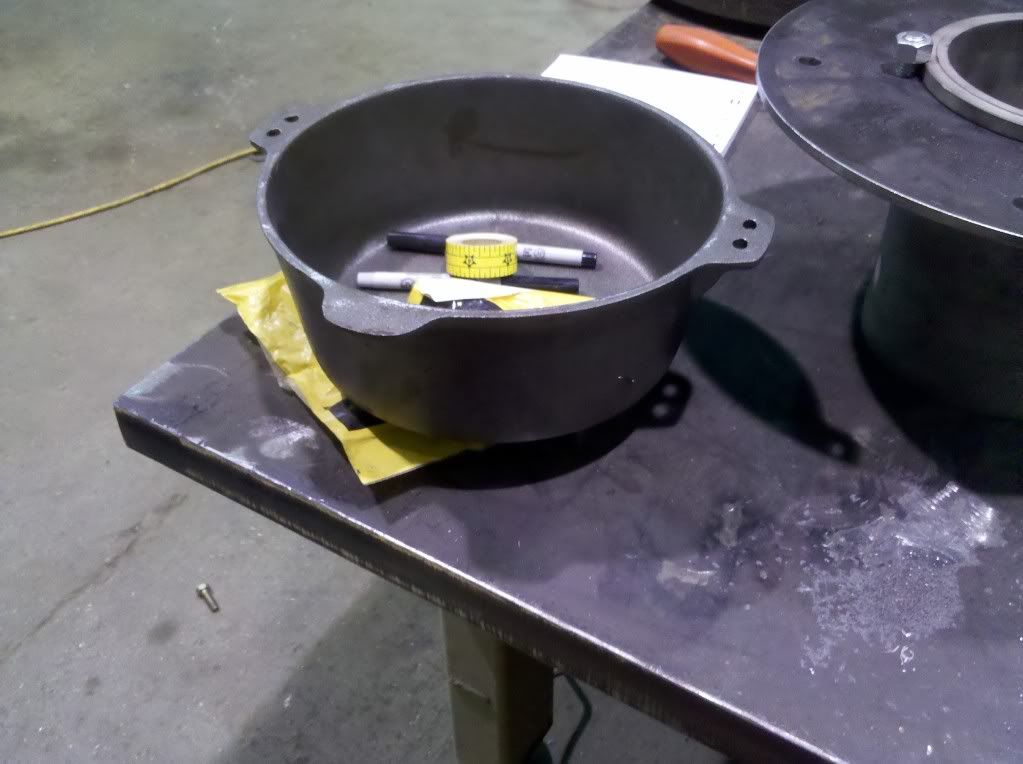
The bottom of the disk
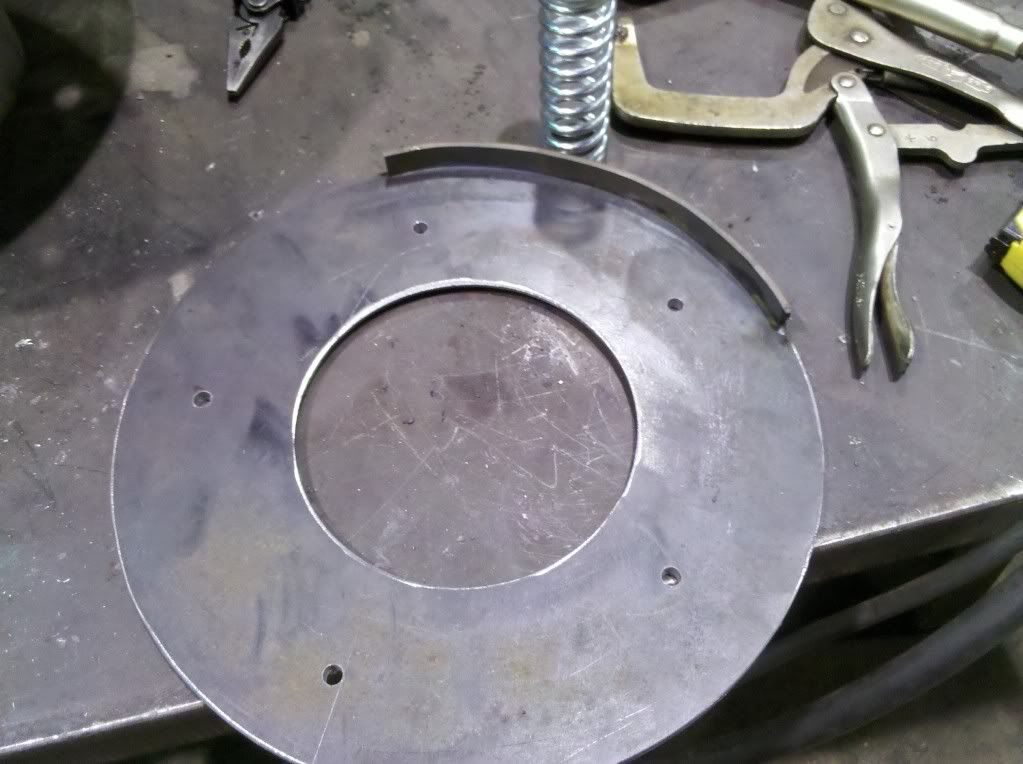
... and the top of the disk.
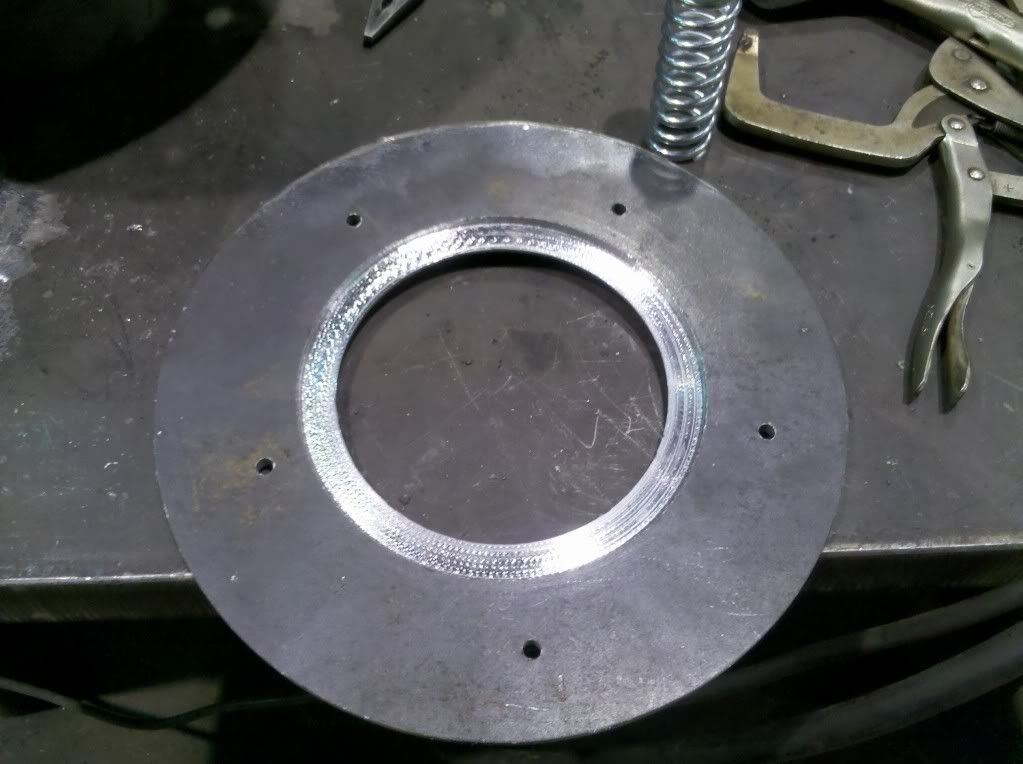
This is a pic of the burner assembly less the frame. The top plate will be bolted to the lower brake drum.
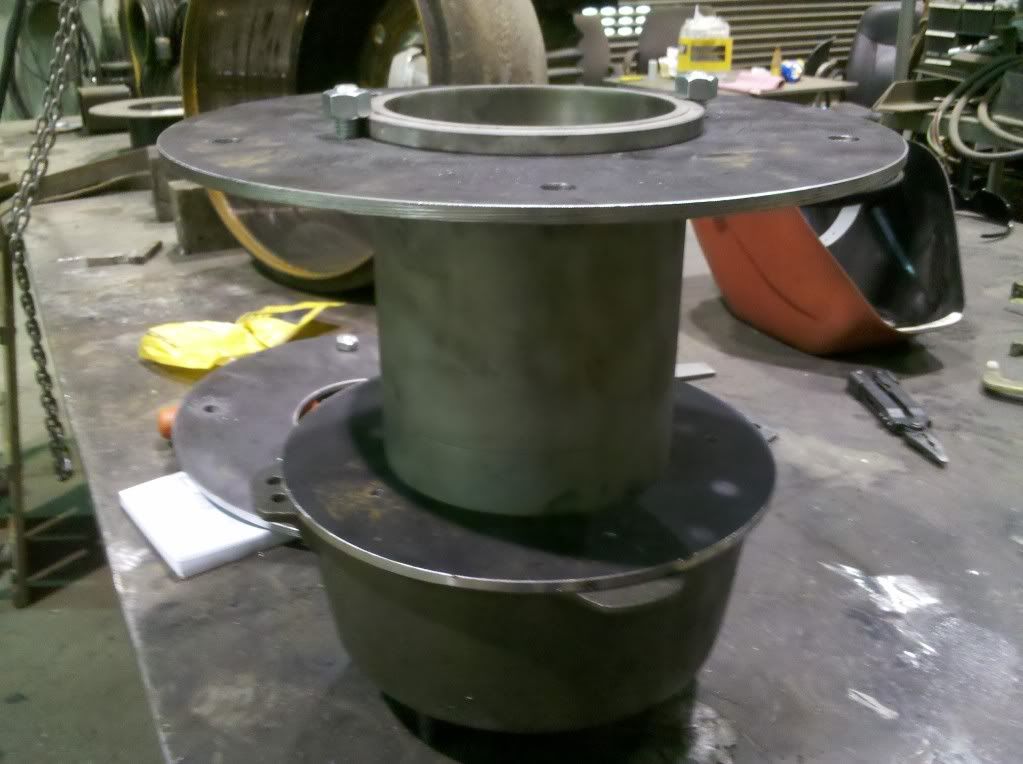
The frame has a spring and a handle to release the pot. The spring pushes directly on the bottom of a plate that the pot sets on. The plate is attached to a hinge that is welded to a cross member on the back of the frame. There are two dowels one for the bottom of the spring and one for the plate to keep it in place. The plate for the bottom drum has 1 inch spacers for bolt clearance, welded to the frame. The drums setting next to the frame are setting as they will once the frame and drums are mated.
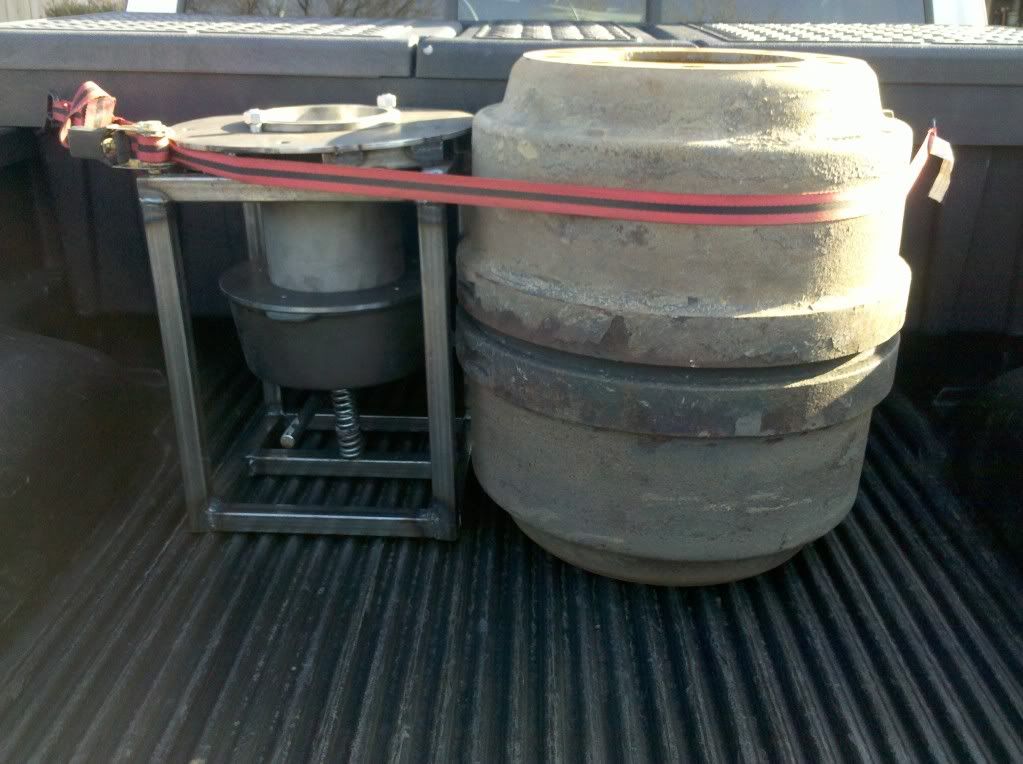
I need to widen the front of the frame; it is difficult to clear the pot. I also need to drill the cylinder for vent holes and install a baffle in the drums to deflect the draft out to the drums. Then I can weld on the draft tube, paint and install.Statistics: Posted by Dngspot — Tue Dec 28, 2010 10:03 pm
]]>